News Details
ICL, a British chemicals company, is using the RFID solution provided by CoreRFID to record the looping and restitution of the recycled barrel and its status. The scheme can improve the efficiency of the company and ensure that the damaged or expired collection of barrels is not used for transport of chemicals. Employees are able to achieve this by using RFID handheld readers with built-in cameras, using RFID handheld readers with built-in cameras, to access the collection barrel in and out of the company.
At present, the company is also ready to use the RFID solution to carry out a comprehensive inventory of barrels.
ICL mainly handles water treatment, detergent and other chemical packaging, and has six different factories in the UK. The company USES a medium-size bulk assembly barrel (IBCs) and a pump box (used for filling the container inside a customer's tank) to deliver goods to customers throughout the country. An IBC can carry 1000 litres of chemicals. Four years ago, the company began using IBC, and now there are 6, 000 IBC collections on the software database, worth more than half a million euros.
Darren Sharpe, an energy program manager at ICL, said: "the market for chemicals is quite large. ICL used to be a commodities delivery company, and in 2011 it wanted to enter the packaging market, especially after the construction of the group's chlorine-alkali plant.
The IBC is a very important investment for companies, Sharpe said. However, it is also difficult for companies to track their locations in and out of six UK factories and customers.
Chemical transport should strictly comply with UK pollution control laws and regulations and the control of major hazardous products. In 2011, ICL started using IBC transport chemicals under current regulations, and the IBC will be placed on customers until the chemicals are exhausted. The company needs to closely track the transport and return of IBC. To ensure damage, the IBC that exceeds the inspection date or reaches the service life is not used.
Initially, the ICL attached a non-rfid plastic tag with a printed ID number on each collection barrel, and employees had to manually record the ID Numbers. In this way, the company staff can identify each print ID number to ensure that the cask can be shipped or returned. If the employee finds any damage to the collection barrel, they can fill in a written report and attach the ID number on the bucket label. However, Sharpe says the process is time-consuming and the tags are not durable enough in the environment. He explained: "the process of IBC identification and life inspection is very time-consuming. The introduction of RFID tracking systems simplifies this process and improves efficiency.
Now, employees can access each IBC information with a handheld reader. RFID technology can also allow employees to enter details, such as collecting barrels or returning dates, recording damage information, etc.
To achieve this, employees installed permanent Omni - ID Exo 600 tags over each IBC metal frame. Each reinforcement tag has a unique ID number that binds the IBC information (serial number, weight, the next inspection date, the company to which it belongs). This information is stored on CoreRFID software on the cloud server. The RFID system only tracks the asset itself, and the contents and the customer's name are stored in the relevant company's management system.
After filling the bucket with a customer's product, the shovel loads it onto the truck. Before the truck leaves, the staff USES the Atid AB700 handheld reader to enter the transport information (such as the customer and its location) and read the label within 3 meters. The CoreRFID firmware on the reader compares the set of the bucket ID number and the history record, if any exception is displayed on the screen. If there is no abnormality, the driver can deliver the goods to the customer.
Every day before work, employees need to upload the reader data to CoreRFID software to update the status of the assembly barrel.
When the customer returns the empty container, the employee needs to read the tag ID number with the handheld reader and check the IBC information again. If the IBC is found to be damaged, they will need to use built-in camera photography, which will also be saved with the tag reading data. Before leaving work, the information will be uploaded to the server, and if there are any questionable assets, the company can learn from the management system and file a claim with the customer.
Office workers can also check the location of the collection by managing the software. In this way, they can find that IBC, which has been too long to leave the ICL facility, can be judged to be missing.
Richard Harrison, director of technology sales at CoreRFID, said the biggest challenge in the RFID installation process was finding hardware that was suitable for the environment and also for users. Eventually, the company chose the Omni - ID tag, not only because it works well in the metal environment, but also because of the impact of the label.
In the past few months, ICL has commissioned CoreRFID to design an RFID scheme to test the integrity of all storage tanks in the company. At present, the system is in the process of installation and will be used to provide security critical inspection records to ICL. So far, the company has attached Exo 600 tags on 6,000 IBC and 300 belt pumps to make it easier for employees to read live data.
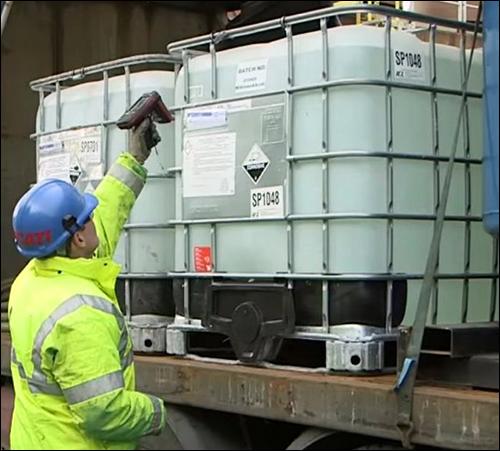
At present, the company is also ready to use the RFID solution to carry out a comprehensive inventory of barrels.
ICL mainly handles water treatment, detergent and other chemical packaging, and has six different factories in the UK. The company USES a medium-size bulk assembly barrel (IBCs) and a pump box (used for filling the container inside a customer's tank) to deliver goods to customers throughout the country. An IBC can carry 1000 litres of chemicals. Four years ago, the company began using IBC, and now there are 6, 000 IBC collections on the software database, worth more than half a million euros.
Darren Sharpe, an energy program manager at ICL, said: "the market for chemicals is quite large. ICL used to be a commodities delivery company, and in 2011 it wanted to enter the packaging market, especially after the construction of the group's chlorine-alkali plant.
The IBC is a very important investment for companies, Sharpe said. However, it is also difficult for companies to track their locations in and out of six UK factories and customers.
Chemical transport should strictly comply with UK pollution control laws and regulations and the control of major hazardous products. In 2011, ICL started using IBC transport chemicals under current regulations, and the IBC will be placed on customers until the chemicals are exhausted. The company needs to closely track the transport and return of IBC. To ensure damage, the IBC that exceeds the inspection date or reaches the service life is not used.
Initially, the ICL attached a non-rfid plastic tag with a printed ID number on each collection barrel, and employees had to manually record the ID Numbers. In this way, the company staff can identify each print ID number to ensure that the cask can be shipped or returned. If the employee finds any damage to the collection barrel, they can fill in a written report and attach the ID number on the bucket label. However, Sharpe says the process is time-consuming and the tags are not durable enough in the environment. He explained: "the process of IBC identification and life inspection is very time-consuming. The introduction of RFID tracking systems simplifies this process and improves efficiency.
Now, employees can access each IBC information with a handheld reader. RFID technology can also allow employees to enter details, such as collecting barrels or returning dates, recording damage information, etc.
To achieve this, employees installed permanent Omni - ID Exo 600 tags over each IBC metal frame. Each reinforcement tag has a unique ID number that binds the IBC information (serial number, weight, the next inspection date, the company to which it belongs). This information is stored on CoreRFID software on the cloud server. The RFID system only tracks the asset itself, and the contents and the customer's name are stored in the relevant company's management system.
After filling the bucket with a customer's product, the shovel loads it onto the truck. Before the truck leaves, the staff USES the Atid AB700 handheld reader to enter the transport information (such as the customer and its location) and read the label within 3 meters. The CoreRFID firmware on the reader compares the set of the bucket ID number and the history record, if any exception is displayed on the screen. If there is no abnormality, the driver can deliver the goods to the customer.
Every day before work, employees need to upload the reader data to CoreRFID software to update the status of the assembly barrel.
When the customer returns the empty container, the employee needs to read the tag ID number with the handheld reader and check the IBC information again. If the IBC is found to be damaged, they will need to use built-in camera photography, which will also be saved with the tag reading data. Before leaving work, the information will be uploaded to the server, and if there are any questionable assets, the company can learn from the management system and file a claim with the customer.
Office workers can also check the location of the collection by managing the software. In this way, they can find that IBC, which has been too long to leave the ICL facility, can be judged to be missing.
Richard Harrison, director of technology sales at CoreRFID, said the biggest challenge in the RFID installation process was finding hardware that was suitable for the environment and also for users. Eventually, the company chose the Omni - ID tag, not only because it works well in the metal environment, but also because of the impact of the label.
In the past few months, ICL has commissioned CoreRFID to design an RFID scheme to test the integrity of all storage tanks in the company. At present, the system is in the process of installation and will be used to provide security critical inspection records to ICL. So far, the company has attached Exo 600 tags on 6,000 IBC and 300 belt pumps to make it easier for employees to read live data.
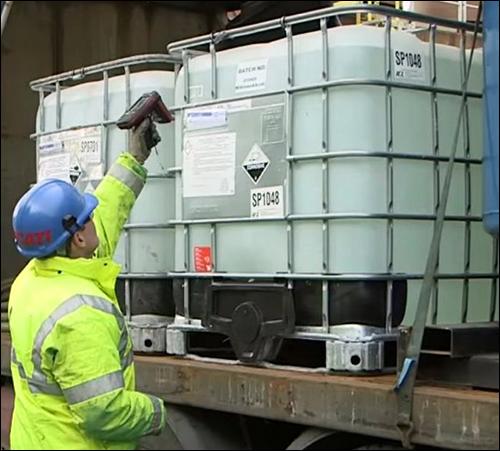